Manufacturing companies often aim for perfection, and for good reason—quality and precision are crucial in this industry. In manufacturing, perfection isn’t just a goal—it’s a necessity.
Accuracy and quality are non-negotiable.
But what happens when the pursuit of perfection paralyzes progress?
There’s a fine line between minimizing mistakes and creating a culture that scares them. Let’s see the fine line between perfection and progress in the workplace:
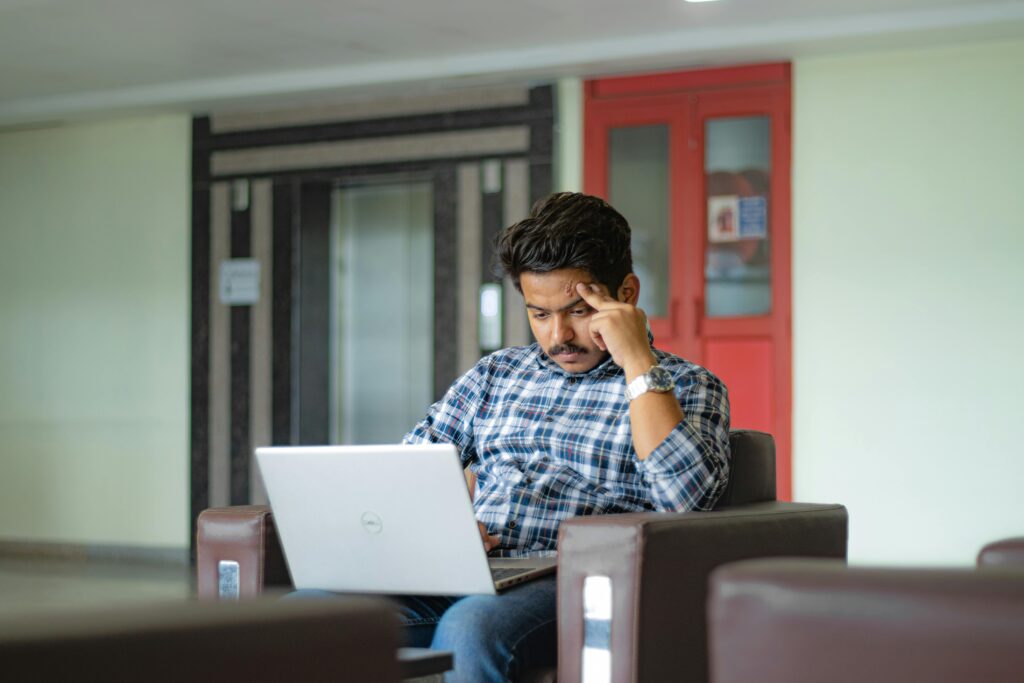
The Dangers of Chasing Perfection:
- Micromanagement: Constantly overseeing every detail to avoid mistakes can lead to control issues
- Example: Imagine a high-precision electronics factory, where managers oversee every step of the assembly process, from the soldering of tiny components to the testing phase. While ensuring quality is important, this intense scrutiny causes workers to feel like they can’t make decisions on their own, leading to slower production and reduced morale. The fear of stepping out of line results in a lack of initiative and innovation from the team.
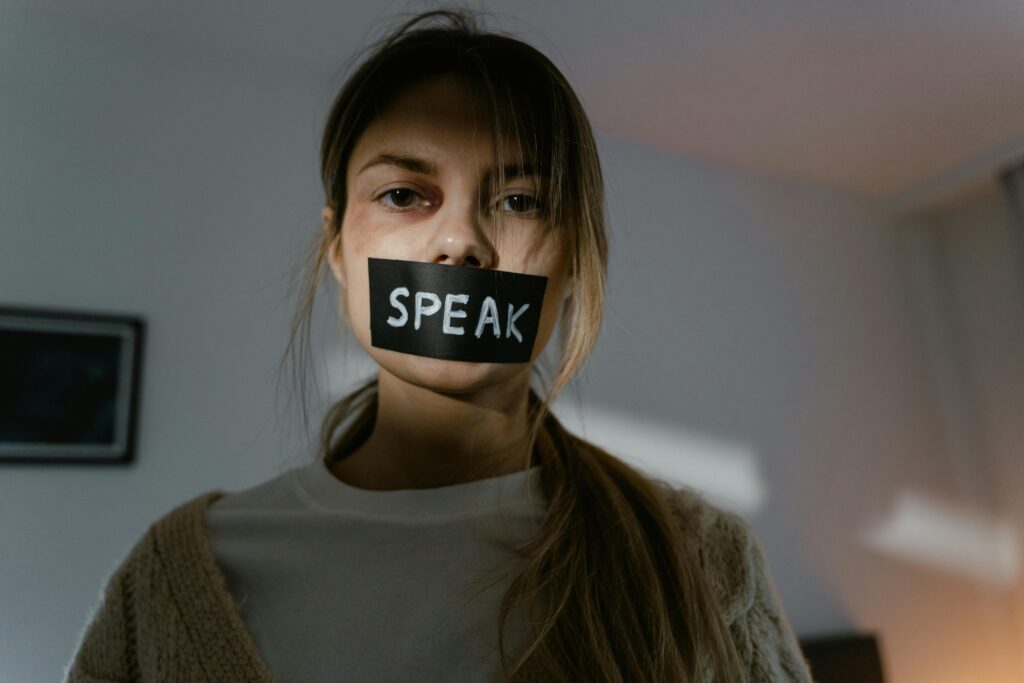
- Fear of speaking up: Employees become afraid to share their ideas or take initiative.
- Example: One of our client is an automotive plant. The management complains about some workers who notice flaws in a batch of parts but ted to not speak up because they are afraid of getting in trouble. The workers cared more about not getting blamed than making sure the problem was fixed. So, they ignore it. Later, the flaw turns into a bigger issue, and the company has to pay a lot to fix it. If the workers could feel safe to speak up sooner, the company could solve the problem before it gets worse.
- Missed opportunities: Focusing solely on perfection can stifle innovation and hinder growth.
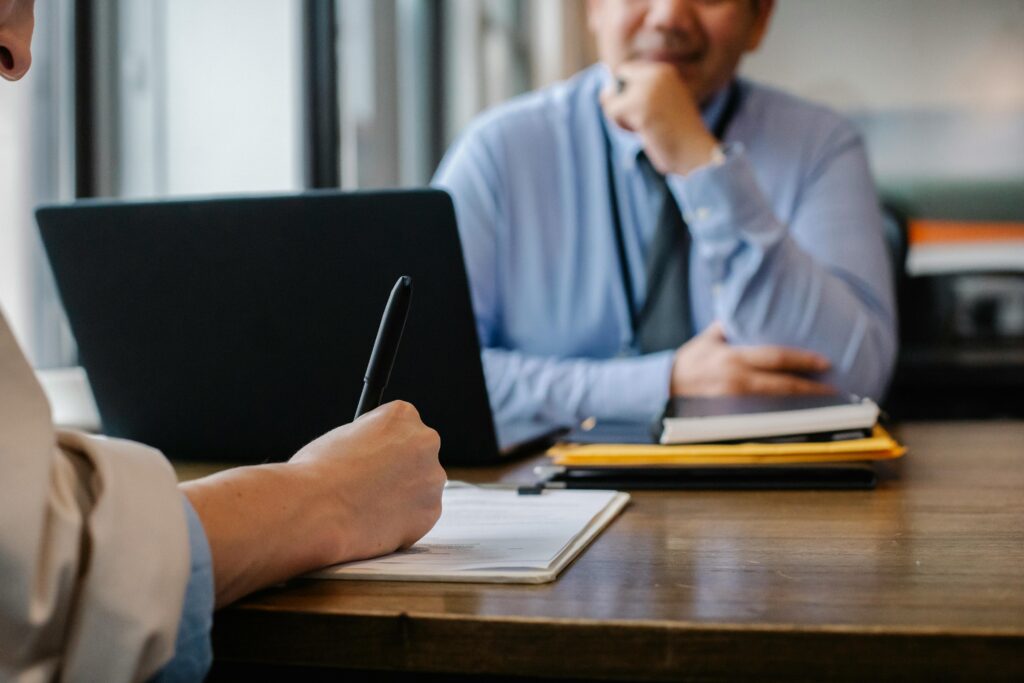
The Power of Empowerment
In many manufacturing companies, the top management is aware of the challenges, and frontline workers often spot the issues. However, it’s middle management that plays a crucial role in bridging the gap. Too often, middle managers feel disempowered to make decisions that could help their teams grow and innovate. Empowering them to take charge can create a ripple effect, unlocking progress across all levels of the organization.
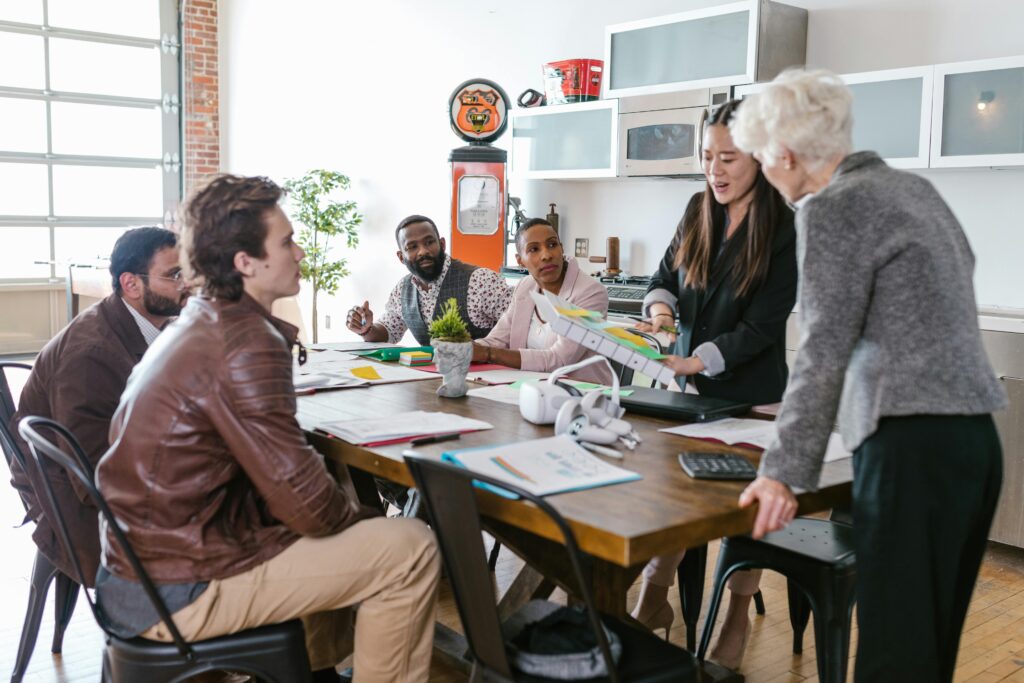
The middle management in your plant should have the following skills and mindsets:
- Learning from mistakes: When mistakes are viewed as opportunities, teams can grow and improve.
- Ownership and continuous improvement: Empowering employees fosters a culture of accountability and progress.
- Driving solutions: A focus on progress leads to innovative solutions and increased profitability.
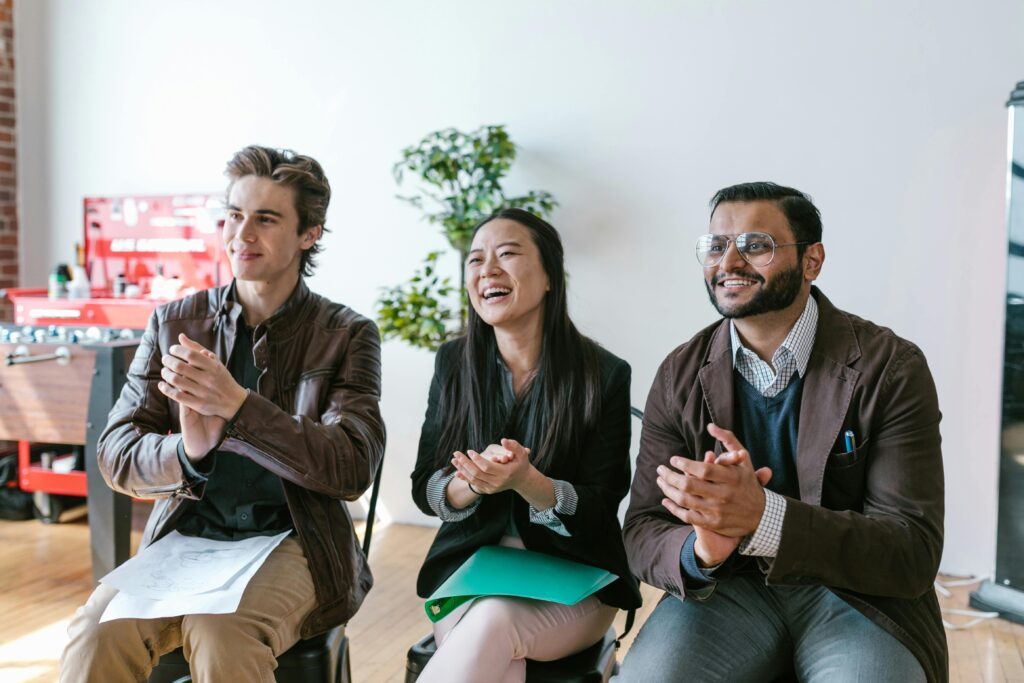
Shifting the Mindset:
- It’s not about avoiding mistakes at all costs—it’s about empowering people to take ownership and make improvements.
- To start changing your culture, top leaders can take the first step by encouraging open communication and recognizing the value of mistakes. Hold a meeting where leaders share stories of times they learned from mistakes and how that led to growth. This sets the tone for a culture where learning is valued over perfection. It’s a small shift, but it can have a big impact on building trust and innovation across all levels of the organization.
What’s Holding You Back?
Is your company ready to move from perfection to progress? Imagine the incredible impact of empowering your teams to drive innovation and long-term success. Don’t wait—take the first step toward meaningful change. Book a call today to discover how we can help you transform your company culture and unlock your team’s full potential.
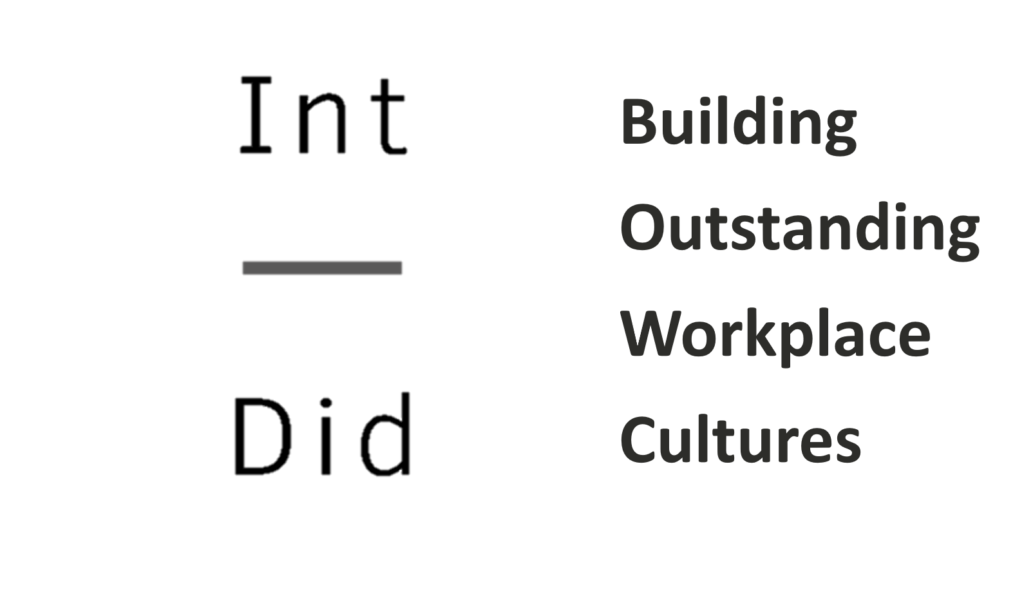
Related Articles
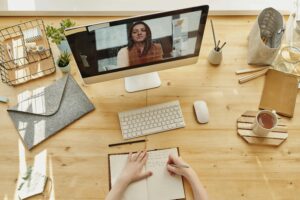
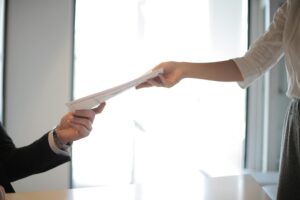
From Résumé to Real-World: How Skill Assessments Improve Hiring Accuracy
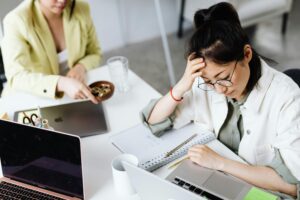